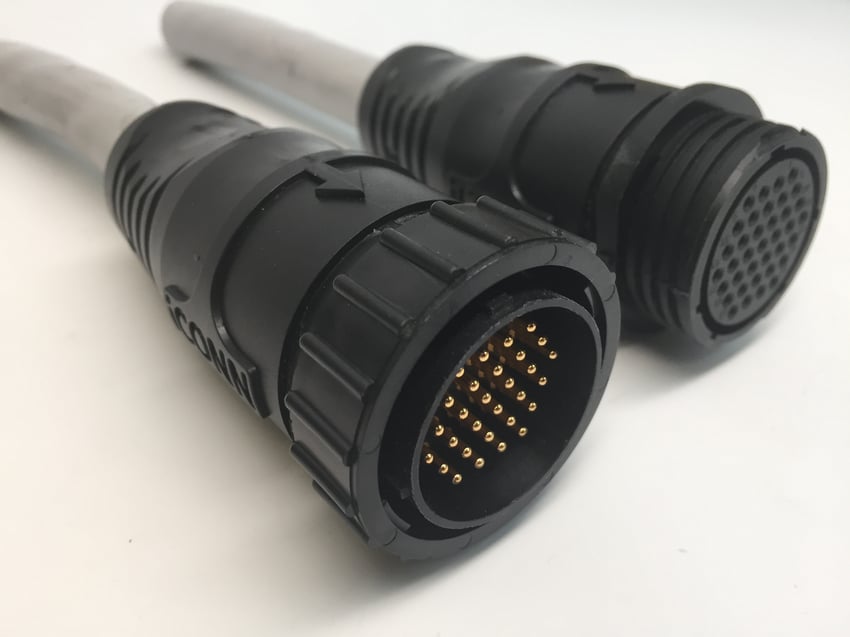
To name every electrical connector type and variation in existence would be like counting grains of sand on a beach – the options are virtually limitless. What we can do instead is to break down electrical connectors into general categories and subcategories to help you understand the expansive inventory of products available to you.
Let’s start by looking at the basics of different connector types, variations, coupling styles, terminal bonds, and more.
3 Basic Electrical Connector Types
A cable connector is a component that gets attached to the end of a cable and allows you to connect to a cable with any port. Below, you will find three main connector types and the devices that they connect to:
- In-line cable connectors – Permanently attached to cable ends, these connectors enable the cable to be plugged into a terminal (either a device or another cable).
- Board-mount connectors – These options are soldered to a printed circuit board (PCB) to allow for cable or wire attachment.
- Panel-mount connectors – These connectors are permanently attached to a piece of equipment, allowing users to connect power or signal cables to a stationary device.
Understanding Connector Variations
All connectors have a mated pair, with these components commonly being referred to as the plug and the receptacle. Each half has a pin and socket contact, and the contacts are made of conductive metal.
- Rectangular connectors – These are ideal for modular machines (factory automation, robotics, transportation, etc.) because they are highly customizable, fit into tight spaces, and easily combine multiple media, such as power, signal, coax, and more.
- Circular connectors – Circular connectors are commonly used for free-hanging connections that pass through a cable tray or connections mounted on a panel. These electrical connectors are also commonly used in rugged environments where IP ratings, EMI/RFI shielding, and other protective measures are required.
When selecting the right electronic connector type, it is essential to consider the surrounding environment. For example, food and beverage companies use circular connectors because their field requires a solution that can withstand high-pressure hoses and will not have areas where food or liquid will get stuck.
Exploring Different Coupling Styles to Ensure Secure Connections
To avoid hazardous situations in your workplace, it is important to have a secure and safe connection between your mated connectors, and coupling mechanisms ensure these secure connections.
Electrical coupling types and styles include:
- Quick connect couplings – These are designed to replace threaded or flanged connections with plastic fittings that allow technicians to replace lines quickly and easily.
- Snaplock couplings – These options are compression couplings designed for quick release and simple, tool-free installation.
- Threaded couplings – Units of this type have internal male and female threads (hence the name) that screw together to form a strong, seamless connection.
- Bayonet couplings – These components involve plugging and twisting a male device with contact pins into a female end with matching sockets. An L-shaped slot and spring mechanism on the female end locks the connection into place.
- Push-pull couplings – These use a strong locking mechanism to prevent accidental disconnects. The coupling can only be released by squeezing the connector body.
When choosing a coupling style for your cable connector, it is essential to consider technical requirements, environmental conditions, ergonomics, and the required number of mating cycles.
Terminal Bonds
As you consider cable connector types, it is also important to determine the terminal bond that you need. Crimping is easier to do than soldering, but it requires a tool that is specific to the type of contact used. For this reason, it is best to purchase crimped electrical connectors off the shelf.
- Crimping – This process involves adjoining a wire to a wire or a wire to a terminal by using a tool or machine to deform and compress metal parts until they form a gas-tight bond.
- Soldering – This involves the process of adjoining a wire to an electrical component using solder material that is melted onto the joint, creating a permanent bond while simultaneously acting as a conductor of electricity.
Specialized Electrical Connector Types
The type of electrical connector you purchase or develop will depend entirely on the application, electrical requirements, mechanical needs, and environmental factors.
- Rugged connectors – These are overmolded with plastic resin to withstand extreme temperatures, abrasion, tension, and other elements that can put strain on a connector design.
- Wet-mate connectors – These units are engineered with niobium technology that acts as a water-friendly insulator, making the cable assembly truly waterproof (not just water-resistant).
Connectors can be purchased off-the-shelf in standard designs and configurations. Standard connectors can also be modified to meet unique application requirements or custom designed from scratch to ensure the perfect fit and performance.
Use iCONN Systems for All of Your Custom and Turnkey Part Needs
iCONN Systems is a company founded by engineers who develop, prototype, and manufacture industry-standard and custom-engineered connectors. We treat our customers as partners by asking key questions to understand your needs, and then recommend the best solutions so you can focus on the project at hand, rather than cable assembly failure.
Connect with Us Today!
If you’re looking for turnkey or custom cable connectors, iCONN Systems is your destination. For more information about types of connectors or our abilities in customization, be sure to reach out to our experts today.